- Process Overview: The process typically starts with a digital 3D model of the product design. This model is then used to guide the manufacturing of physical prototypes using rapid prototyping technologies. Depending on the specific method chosen (like 3D printing or CNC machining), the prototype is built layer by layer or machined from a solid block of material.
- Types of Rapid Prototyping Technologies:
- 3D Printing/Additive Manufacturing: This involves building up layers of material to create the prototype. It’s versatile and suitable for producing complex geometries quickly.
- CNC Machining: Computer Numerical Control (CNC) machines are used to remove material from a solid block to form the prototype. It’s ideal for creating prototypes from engineering-grade materials.
- Rapid Injection Molding: While more traditional than 3D printing, it allows for the rapid production of plastic prototypes using molds that are quickly fabricated.
- Vacuum Casting: This method involves creating silicone molds from a master model and then casting prototype parts in polyurethane resin. It’s suitable for producing small batches of prototypes that mimic the final product.
- Materials Used: A wide range of materials can be used in low volume rapid prototype manufacturing, including various plastics, metals, ceramics, and composites. The choice of material depends on factors such as strength requirements, surface finish, and functional testing needs.
- Benefits:
- Reduced Time to Market: By quickly iterating through prototypes, companies can accelerate their product development cycles and respond faster to market demands.
- Cost Savings: Compared to traditional prototyping methods, rapid prototyping can save costs on tooling and setup, especially when producing small quantities of prototypes.
- Design Optimization: Engineers and designers can easily modify designs based on testing and feedback, leading to optimized products before mass production.
- Challenges:
- Material Limitations: Rapid prototyping materials may not always have the same properties as final production materials, which can affect testing accuracy.
- Post-Processing Requirements: Depending on the chosen method, prototypes may require additional finishing processes to achieve desired surface finishes or mechanical properties.
- Scalability: While ideal for low volumes, rapid prototyping methods may not be as cost-effective for large-scale production.
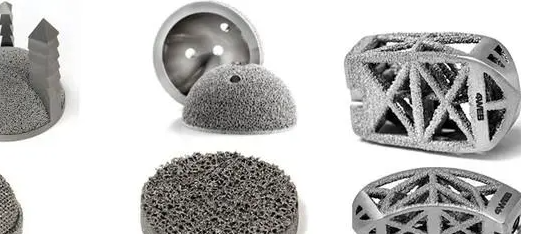