Investment Casting:
- Wide Range of Metals: Investment casting supports a broad spectrum of metals and alloys. Common materials include:
- Steel: Various grades including carbon steel, stainless steel, and tool steel.
- Aluminum: Different alloys such as 6061, 7075, and others.
- Titanium: Known for its strength-to-weight ratio and corrosion resistance.
- Bronze and Brass: Used for applications requiring corrosion resistance and aesthetic appeal.
- Nickel-Based Alloys: Suitable for high-temperature applications and corrosive environments.
- Exotic Alloys: Investment casting can accommodate more specialized materials like cobalt-chromium, Inconel, and other superalloys used in aerospace and high-performance applications.
- Material Properties: The casting process retains the inherent properties of the metal, such as strength, ductility, and heat resistance, making it suitable for demanding applications where material performance is critical.
- Material Consistency: Investment casting produces parts with consistent material properties throughout, which is advantageous for structural integrity and reliability in critical components.
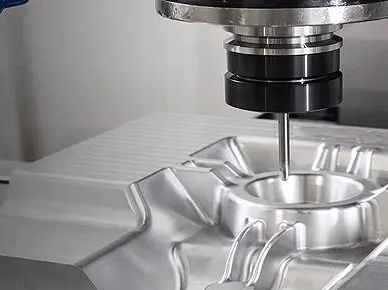
CNC Milling:
- Similar Range of Materials: CNC milling also supports a wide array of materials, similar to investment casting:
- Metals: Steel, aluminum, titanium, brass, bronze, and various alloys.
- Plastics: Acrylics, polycarbonates, nylon, and more.
- Composites: Carbon fiber, fiberglass, and laminates.
- Material Properties: CNC milling can maintain the material properties of metals and plastics but may introduce residual stresses due to the machining process. However, advanced techniques like CNC grinding can mitigate some of these effects.
- Material Removal: CNC milling can handle tougher materials like hardened steel and titanium, which may be more challenging to cast with investment casting.
- Material Availability: The availability of raw materials is generally not a constraint for CNC milling, allowing for flexibility in sourcing specific materials based on application requirements.
Choosing Based on Material Flexibility:
- Complexity and Design: If the design requires intricate details or complex internal features, investment casting may offer more flexibility with a broader range of alloys, especially for parts where maintaining material properties is crucial.
- Volume and Cost: For lower volumes of specialized parts or prototypes where material choice is critical, investment casting provides flexibility with exotic alloys. CNC milling is advantageous for larger production runs and when material versatility across a range of conventional metals and plastics is sufficient.
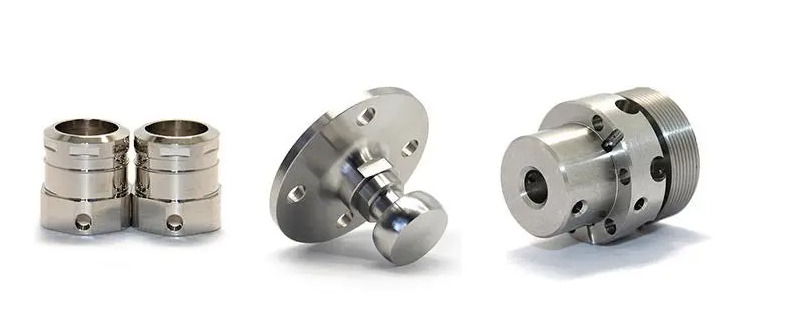