Table of Contents
Mineral Casting:
- Material Composition: Mineral casting typically consists of a mixture of natural minerals (like quartz sand or granite aggregates) and a polymer resin binder (epoxy or polyester). The exact composition can vary, but it generally aims to optimize properties such as stiffness, vibration damping, and thermal stability.
- Properties and Advantages:
- High Rigidity: Mineral castings are known for their high rigidity, which is crucial for maintaining dimensional accuracy and stability in CNC machines and precision instruments.
- Vibration Damping: They exhibit excellent vibration damping properties, which helps in reducing machine vibrations during operation, leading to improved machining accuracy and surface finish.
- Thermal Stability: Low thermal expansion ensures dimensional stability over a wide range of temperatures, making mineral castings suitable for environments with varying thermal conditions.
- Durable and Maintenance-free: Mineral castings are resistant to corrosion, aging, and deformation, requiring minimal maintenance over their operational life.
- Applications:
- Machine Tools: CNC machine beds and frames benefit greatly from mineral casting due to its stability and vibration absorption.
- Metrology Equipment: Used in measuring machines and coordinate measuring systems where precision and stability are critical.
- Medical Equipment: Applications include MRI machines and other sensitive medical devices where stability and vibration control are essential.
Resin Casting:
- Material Composition: Resin casting involves pouring liquid resin (such as epoxy, polyurethane, or polyester) into molds, which then harden and cure to form solid parts. Various additives can be included to modify properties like strength, flexibility, or hardness.
- Properties and Advantages:
- Versatility: Resin casting allows for the production of parts with complex geometries and fine details that may be difficult or costly to achieve with traditional machining methods.
- Lightweight: Resin cast parts are generally lightweight compared to mineral castings and metals, making them suitable for applications where weight reduction is beneficial.
- Cost-effective: Ideal for prototypes and small production runs due to lower setup costs and flexibility in design changes.
- Mold-making: Resin casting is also used extensively in creating molds for subsequent manufacturing processes like injection molding or vacuum forming.
- Applications:
- Prototyping: Rapid prototyping of parts and components to test form, fit, and function before committing to more costly production methods.
- Art and Design: Used in artistic and creative industries for sculptures, decorative pieces, and architectural models.
- Electronics: Encapsulation of electronic components and devices for protection against environmental factors like moisture and dust.
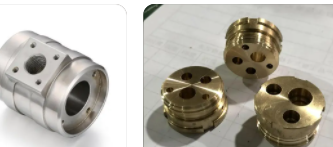
Considerations for CNC Machining:
- Precision Requirements: Mineral casting is preferred for applications requiring high dimensional accuracy and stability, such as CNC machine bases.
- Production Volume: Resin casting is suitable for low to medium production volumes and rapid prototyping due to its cost-effectiveness and flexibility.
- Material Selection: Depending on specific application needs (e.g., mechanical properties, thermal stability), the choice between mineral casting and resin casting can significantly impact performance and overall cost-effectiveness.
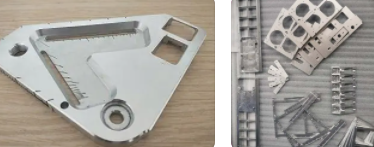