Table of Contents
Prototype Machining
- Material Selection: Steel is chosen for its strength, durability, and machinability. Common types used include stainless steel, tool steel, and alloy steel, each offering different properties suited to specific applications.
- Design Preparation: Before machining begins, the prototype design should be finalized, often in CAD (Computer-Aided Design) software. This includes detailed specifications and dimensions.
- Machining Processes:
- Turning and Milling: CNC (Computer Numerical Control) machines are typically used for precision and consistency.
- Drilling and Tapping: Essential for creating holes and threads.
- Grinding and Surface Finishing: Ensures the prototype meets exact dimensional tolerances and surface requirements.
- Quality Control: Regular checks and measurements ensure prototypes meet design specifications. This may involve dimensional checks, material testing, and surface finish inspection.
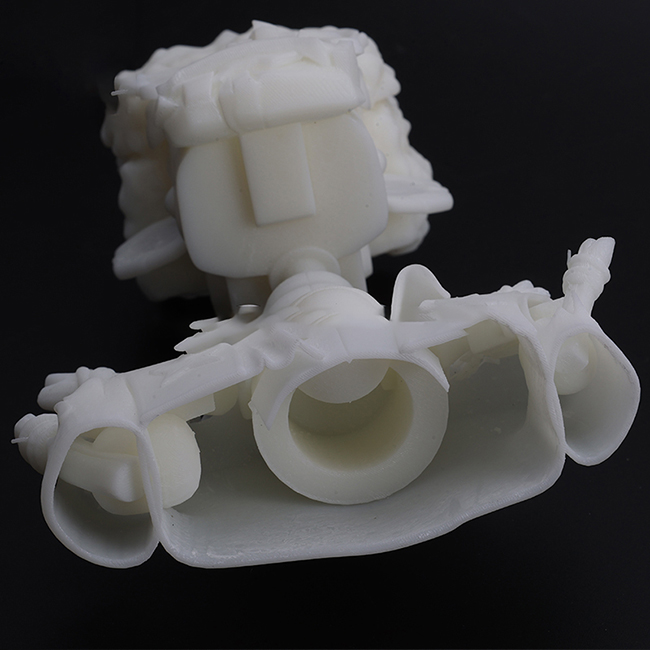
Prototype Tooling
- Tooling Design: Tooling refers to molds, dies, and fixtures necessary for manufacturing prototypes. They are designed to withstand the stresses of production and ensure consistent output.
- Material Selection: Tool steel is often used for prototype tooling due to its hardness and resistance to wear. The specific grade depends on the application requirements.
- Manufacturing Processes:
- Machining: Similar processes as for prototype parts, ensuring precision and reliability.
- Heat Treatment: Enhances the hardness and durability of the tooling.
- Assembly and Testing: Tooling components are assembled and tested to ensure they function as intended.
- Iterative Prototyping: Often, multiple iterations of both the part and tooling are required to refine designs and processes before full-scale production.