Additional Considerations for CNC Milling:
- Tooling and Setup: CNC milling requires programming (CAM/CAD) and setting up the machine, which can be time-consuming for complex parts. However, once set up, it offers rapid production of identical parts.
- Material Removal: CNC milling removes material from a solid block (subtractive manufacturing), which can result in significant material waste, especially for complex parts.
- Flexibility in Design Changes: It’s easier and quicker to make design changes in CNC milling compared to investment casting, especially during prototyping phases.
- Suitability for Prototyping: CNC milling is widely used in rapid prototyping due to its ability to quickly produce functional prototypes that closely resemble the final part.
- Applications: Common applications include aerospace, automotive, medical devices, and consumer electronics, where precision and material versatility are crucial.
Additional Considerations for Investment Casting:
- Tooling and Setup: Investment casting requires creating a wax pattern (tooling) and ceramic mold, followed by the casting process. Initial tooling costs can be higher, but amortized over larger production runs.
- Design Freedom: Offers greater design freedom with minimal constraints on part geometry compared to CNC milling, making it ideal for highly complex parts.
- Material Properties: Investment casting preserves the material properties of the metal used, making it suitable for critical applications where material strength and integrity are paramount.
- Surface Finish: Parts produced by investment casting typically have excellent surface finish, often requiring little to no additional finishing operations.
- Applications: Widely used in industries such as aerospace, automotive, jewelry, and medical implants where complex geometries and high-quality surface finishes are required.
Choosing Between CNC Milling and Investment Casting:
- Volume: For low-volume production or prototyping, CNC milling may be more cost-effective due to lower initial setup costs and faster turnaround times.
- Complexity: For parts with intricate details, thin walls, or complex geometries, investment casting is often preferred due to its ability to produce near-net shape parts with minimal machining required.
- Material Selection: Consider the specific material properties required for your application. CNC milling offers more flexibility in material choice, while investment casting is suitable for a broader range of metals and alloys.
- Cost Analysis: Conduct a thorough cost analysis considering upfront tooling costs, per-unit production costs, and potential savings from reduced material waste and machining time.
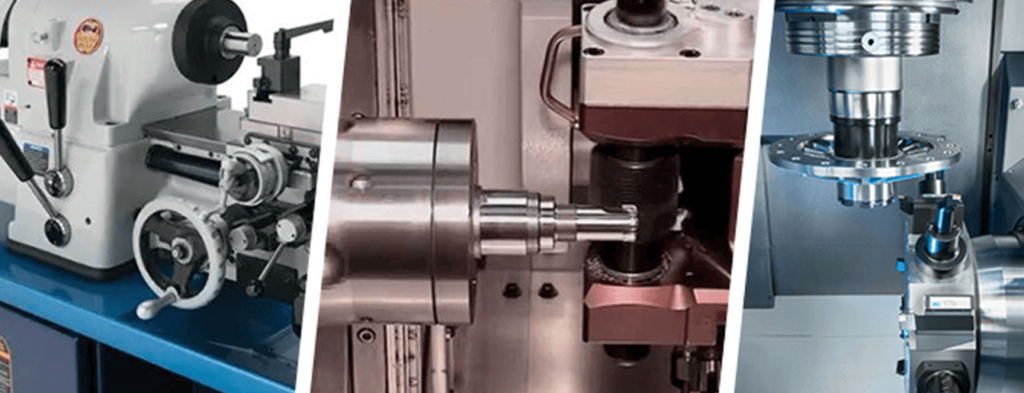