Table of Contents
Brass Casting:
Brass casting is a versatile process used to create intricate shapes and components. Here are some additional points:
- Types of Brass Alloys: Brass is an alloy primarily composed of copper and zinc, but it can also include other elements like lead, tin, or aluminum to modify its properties.
- Applications: Brass casting is used in various industries including automotive, plumbing, marine, and decorative arts due to its corrosion resistance, durability, and aesthetic appeal.
- Casting Methods: Besides sand casting (which is common), brass can be cast using methods like investment casting (lost-wax casting), die casting, and continuous casting, each suited to different production volumes and complexity.
- Advantages: It allows for the production of complex shapes with good dimensional accuracy, repeatability, and minimal machining requirements for certain geometries.
- Post-Casting Processes: After casting, parts may undergo processes such as heat treatment, machining, polishing, and surface finishing to achieve the desired final product specifications.
CNC Machining:
CNC machining is highly precise and widely used across industries. Here are additional details:
- Types of CNC Machines: CNC machines include mills, lathes, routers, grinders, and more, each suited to different machining operations and part geometries.
- Materials: In addition to brass, CNC machining can be used with a wide range of materials including steel, aluminum, plastics, and composites.
- Precision and Tolerances: CNC machining offers high precision, often achieving tolerances within fractions of a millimeter, making it suitable for intricate parts requiring tight dimensional accuracy.
- Versatility: CNC machines can perform a variety of operations including milling, turning, drilling, tapping, and grinding, all controlled by computer programs (G-code) that dictate tool movements and speeds.
- CAD/CAM Integration: CAD software is used for designing parts, while CAM software generates toolpaths and optimizes machining strategies, ensuring efficient and accurate production.
Integration and Hybrid Approaches:
- Combining Processes: Manufacturers often integrate casting and CNC machining to leverage the benefits of each method. For example, casting may be used to produce a part close to its final shape, reducing material waste and machining time.
- Complex Parts: Complex parts with intricate features may require casting for initial shaping followed by CNC machining for fine details and critical tolerances.
- Cost Considerations: Choosing between casting and CNC machining (or their combination) depends on factors such as production volume, material cost, lead time, and required surface finish.
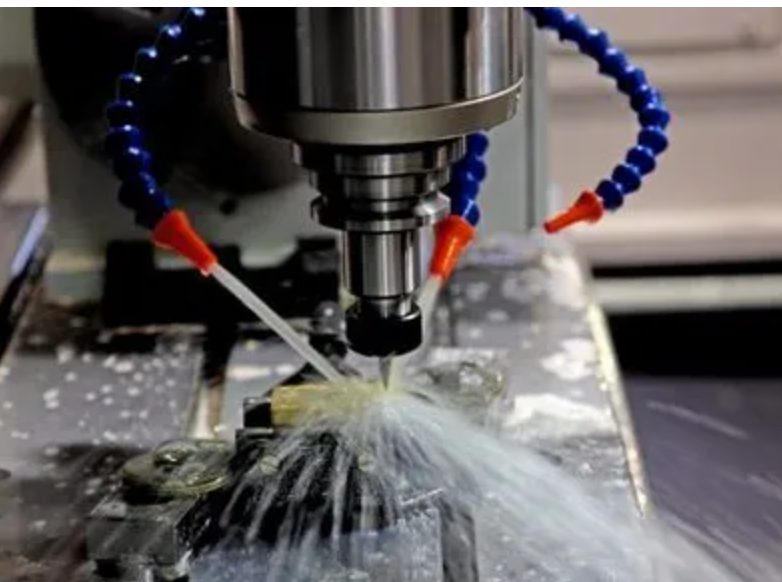